Аддитивные технологии, позволяющие послойно наращивать и синтезировать объекты, уже много лет занимают прочное место в производстве изделий из металлических порошков. Их внедряют «РУСАЛ», «Росатом», ВИАМ, МИТ и многие другие компании, включая коммерческие.
Какие преимущества дают эти технологии и каковы их перспективы в России, особенно с учётом санкций?
Об этом «Про Металл» поговорил с руководителем компании Z-axis Сергеем Кулаковым. Фирма много лет является в России дистрибьютором индустриальных 3D-принтеров.
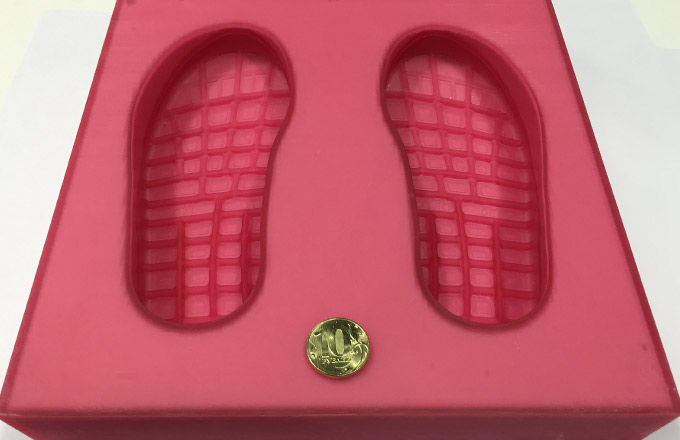
3D металлургия - один из трендов отрасли
– Если мы говорим об изготовлении изделий из металлических порошков при помощи 3D-печати, в каких отраслях они в первую очередь востребованы?
– В медицине, авиационной и космической промышленности в первую очередь, далее в ювелирном производстве, автомобилестроении, обувной промышленности и так далее. Везде, где нужно получить изделие сложной геометрии и высокой точности, включая те, которые затруднительно изготовить с помощью традиционных технологий производства.
Например, активно применяется в стоматологии, где 3D-принтеры позволяют с высокой точностью одновременно выращивать десятки индивидуальных зубных имплантов на одной платформе.
Могу сказать, что спектр практического применения технологии очень широкий. Особенно, если мы говорим об изделиях из металла, напечатанных по технологии SLM (селективное лазерное плавление).
Данная технология позволяет оптимизировать существующие изделия, соединив при печати несколько деталей вместе, которые ранее крепились друг с другом болтами, сваркой или склеиванием, облегчить изделия, что особенно актуально для аэрокосмической отрасли, напечатать инструмент из прочных материалов — например, для горной промышленности, из материала, который тяжело поддаётся механической обработке, вроде вольфрама.
В машиностроении, конечно, тоже применение не сводится только к космосу и самолётам.
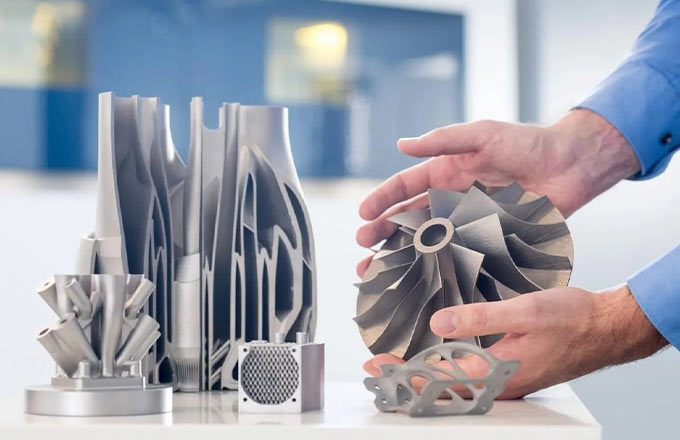
Аддитивные технологии открывают новые возможности в самых разных отраслях
– Была информация, что Китай пытался массово производить с использованием 3D-технологий колёсные пары для железнодорожного транспорта, но качество оказалось довольно низким.
– Если говорить конкретно о 3D для РЖД, то, на мой взгляд, там есть серьёзное поле для применения аддитивных технологий. Например, есть такое понятие, как «реверс-инженерия» («обратное проектирование»).
Вот, допустим, по России бегает множество локомотивов, давно уже снятых с производства (20–30 лет тому назад), запчасти на них уже не производят, документация утрачена, а локомотивы вполне работающие. С помощью «реверс-инжиниринга» можно наладить выпуск этих запчастей, используя 3D-печать!
За рубежом есть хорошие примеры. «Дойчебан» создал центр 3D-компетенций, где использует 3D-принтеры для печати изделий из пластика, металла, изготовления цифровых форм для литья металла изделий для подвижного состава, как при восстановлении старых узлов и агрегатов, так и для усовершенствования существующих.
Компании Siemens печатает бампера трамваев в Германии на промышленных 3D-принтерах. «Алстром» также активно использует 3D-технологии для изготовления и усовершенствования своей продукции, печатая в год несколько десятков тысяч деталей. И РЖД, конечно, за этим следит с большим интересом.
– А помимо точности, какие выгоды даёт использование аддитивных технологий?
– Экономию материала. Когда работает станок с ЧПУ, иногда более 50% металла уходит в стружку. При использовании SLM отходов практически нет, т.к. металлический порошок можно использовать многократно. Кроме этого, 3D-оборудование в разы более экономично по сравнению с традиционным производством. Думаю, что энергоёмкость производства снижается даже не в разы, а на порядок.
3D-оборудование работает круглосуточно с минимальным вовлечением персонала и практически бесшумно.
Кстати, 3D-печать может дать эффект в самых разных отраслях, вроде бы далёких от хайтека — в обувной промышленности, например, где для литья подошв из полиуретана в основном используются импортные алюминиевые пресс-формы, а вот 3D-технология позволяет их изготавливать из высокотемпературного фотополимера с высокой точностью, причём всего за 2-3 дня, вместо 1-2 месяцев.
И ещё, недавно в 3D появились новые инженерные пластики (полиэфирэфиркетон, PEEK / Полиэфирэфиркетон ПЭЭК и др.) с механическими и температурными свойствами металлов, которые подходят для печати функциональных бензино-, масло-, термостойких изделий, что открывает широкие возможности для самых разных отраслей от машиностроения и ВПК до медицины — например, для изготовления вживляемых имплантатов вместо титановых.
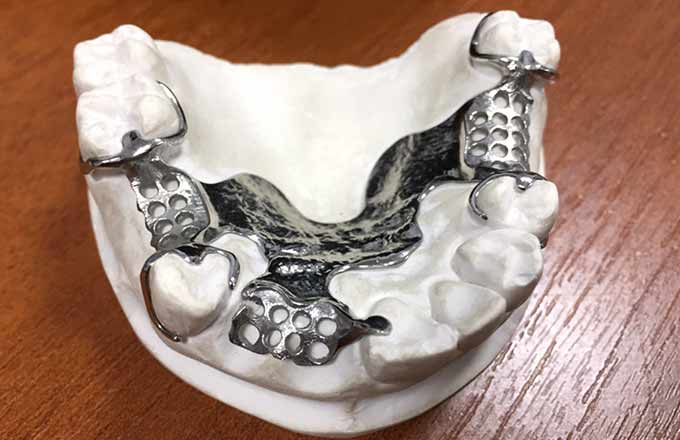
Какая прелесть вставная челюсть. Дорогая только и сложная штука. А с 3D все может быть проще и дешевле
– Аддитивные технологии — тема передовая, но уже не очень-то новая. Работы идут по ней с 90-х годов прошлого века. А Россия в этом плане где находится?
– Я бы так сказал, что если взять технологию лазерного спекания металлического порошка SLM, то Германия — №1, её догоняет весь мир, включая и Россию на вторых-третьих ролях. Перспективы догнать есть, но нужны серьёзные инвестиции. И догнать реально, т.к. технология SLM имеет ограничения, связанные с мощностью лазера, свойствами металлов и прочим, и если принципиального прорыва в SLM не произойдёт, то потихоньку догоним. КНР ведь уже практически догнала!
– В России ведутся собственные научно-технические разработки в данной области?
– Да, разумеется, и даже своё оборудование производится. Сегодня на российском рынке 3D-принтеров, печатающих металлом по технологии SLM, чуть более 200 единиц оборудования (для информации — самый недорогой аппарат стоит не менее 10–12 млн руб., а дорогие и до 200 млн и выше), из которых около 70% поставлено из Германии / Европы и США, 15–20% — отечественного производства, около 10% — из КНР.
Безусловно, изучение технологии ведётся и РФ. В первую очередь я бы вспомнил «РусАт» (ООО «Росатом — Аддитивные Технологии») — мощный отраслевой интегратор, объединяющий усилия дочек атомной корпорации в данной сфере и начавший производство своих 3D-принтеров, ВИАМ (Институт авиационных материалов), у которого современное импортное SLM оборудование.
Они, помимо прочего, заняты крайне важным делом — созданием отраслевых стандартов для изделий, изготовленных с помощью аддитивных технологий, чтобы они могли спокойно производиться на различных отечественных предприятиях.
«РУСАЛ», который является ведущим мировым производителем алюминиевых порошков для 3D-печати по технологии SLM и экспортирует его в многие страны мира, включая Европу и США.
В последние годы в нашей стране появилось много сильных 3D-кафедр в ВУЗах: МГТУ им. Баумана, МАИ, Питерский и Московский политехнические университеты, УГАТУ (Уфа), Национальный исследовательский технологический университет МИСиС, Пермский национальный исследовательский Политехнический университет, Дальневосточный федеральный университет и многие другие.
Из коммерческих структур хотелось бы отметить Казанский центр цифровых технологий, который одним из первых в стране начал изготовление форм для литья металла цифровым способом, применив технологию биндерджеттинг (binderjetting).
Литейная форма размером до 1,4 м3 при помощи такой технологии печатается менее чем за сутки (вместо 2-3 месяцев, которые нужны для изготовления её традиционным путём). Есть и много других центров аддитивных технологий, включая ЦАТ «Ростеха», уже упомянутого МИСиС, «РУСАЛ», ЦТКАТ (Воронеж), ЦАТ в Троицке и другие.
Нужно отметить, что сегодня, благодаря работе правительства РФ и частной инициативе, молодое поколение имеет возможность познакомиться с аддитивными технологиями уже в школе.
В рамках Федеральной программы «Точка роста» в учебные заведения страны было поставлено несколько тысяч 3D-принтеров и многие преподаватели их активно используют для обучения школьников азам 3D-печати. Эту практику, считаю, надо обязательно развивать.
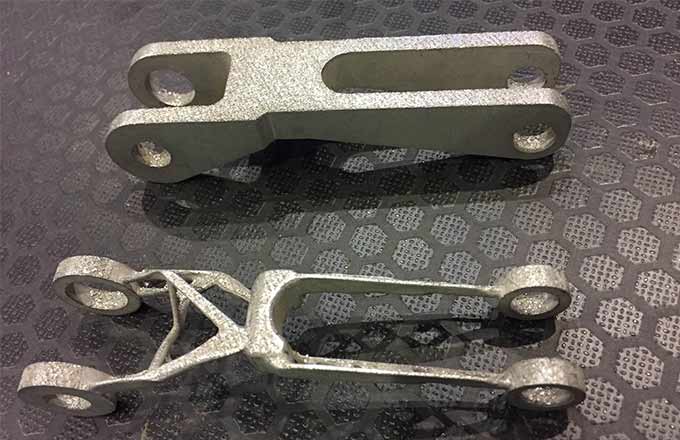
Аддитивные технологии должны изучаться уже со школьной скамьи, если Россия хочет стать передовой страной
– Сейчас против России ввели санкции. Значит, западное оборудование по этому направлению мы больше не увидим? Может ли Китай предоставить адекватную замену?
– Боюсь, что вы правы в отношении оборудования, поставляемого из Германии, США, Франции и других западных стран. Пока санкции не отменят — поставок, скорее всего, не будет, особенно во время операции на Украине. Что же касается КНР, там есть уже рабочее оборудование, которое было скопировано с лучших мировых образцов, в частности SLM-принтеры, которые скопировали с лидеров индустрии EOS, SLM Solutions и других.
Но, к сожалению, есть, и некоторое отставание. Например, можно вспомнить метод 3D-печати, называемый биндерджеттинг-металлом. Эта технология похожа на печать на струйном принтере: слой за слоем на материал (мелкодисперсный порошок) накладывается связующее вещество, которое закрепляет порошок, связующее потом выпаривается, а металл спекается в высокотемпературной печи.
Это если мы говорим именно о металлических порошках, среди которых нержавеющая сталь, карбид вольфрама, титан, медь и т.д., однако с помощью этой технологии можно печатать и многими другими материалами — перспективная технология.
Её изобрели в Германии и США, в MIT, а Китай находится в процессе отработки скопированных образцов, но пока эту работу ещё не завершил. И с нами, значит, поделиться таким оборудованием не может.
Конечно, очень хочется надеяться, что мировой конфликт быстро разрешится и санкции ослабят. Если же нет, придётся что-то придумывать самим или покупать в других странах. Некоторые наработки, как я уже сказал, в России есть. Включая фирмы, которые производят оборудование для индустриальной 3D-печати. Но они остро нуждаются в инвестициях, поскольку то, что в РФ в данную сферу инвестировали в последние десятилетия, было недостаточным в сравнении с Западом и Китаем.