От редакции. Когда мы говорим и пишем о «зелёной металлургии», то, как правило, представляем себе нечто эпохальное, например, огромные железнодорожные составы с рулонами стали, которые пахнут озоном и уносятся куда-то в сторону рая. Возможно, это когда-то и наступит.
На самом деле понятие «зелёной металлургии» гораздо более многогранное. Оно включает в себя не только сам процесс выплавки стали, но и огромное количество вспомогательных производственных процессов, каждый из которых тоже должен соответствовать всем нормам защиты окружающей среды. Для «зелёной» металлургии нужна «зелёная» электроэнергия, «зелёная» логистика, «зелёная» эксплуатация наконец.
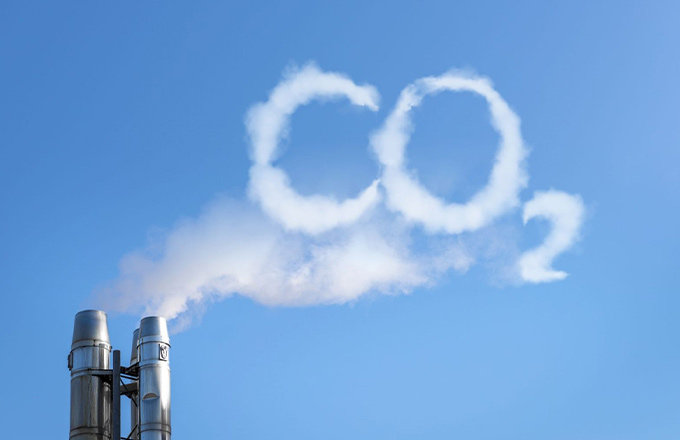
Для «зелёной» металлургии нужна «зелёная» электроэнергия, «зелёная» логистика и «зелёная» эксплуатация.
А в качестве конечного продукта должны получиться, например, экологически чистые инструменты для строительства и ремонта: свёрла, фрезы, резцы. Останется только подсоединить к такой экодрели или экоперфоратору промышленный пылесос из тех, что в основном делают в Германии, и любая стройка будет сравнима с возделыванием вишнёвого сада по своей безвредности для окружающей среды. Это, конечно, утрировано, но цель именно такая.
Отраслевой журнал «Stahl und Eisen» (Германия) публикует материал о промышленной кооперации между немецким торгово-логистическим концерном Heine + Beisswenger, австралийской сталелитейной компанией GMH Group и шведской производственной компанией Sandvik Coromant, которая как раз занимается изготовлением инструмента для строительства и ремонта. Предлагаем его перевод.
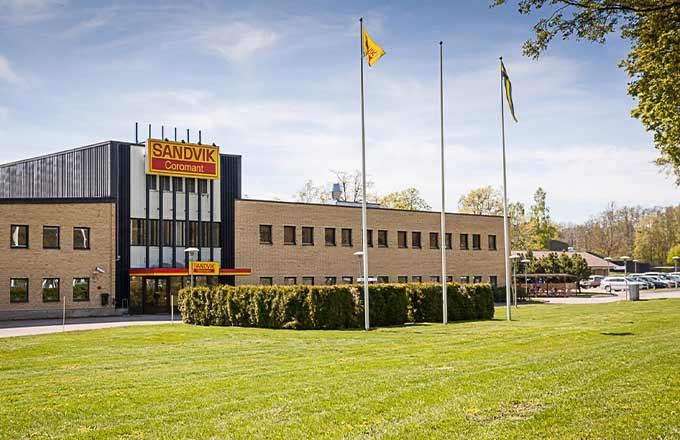
Даже внешний облик компании Sandvik Coromant подчеркивает ее экологичность.
С конца 2021 года компании Heine + Beisswenger (H+B), GMH Group и Sandvik Coromant работают над созданием цепочки создания стали с минимально возможным содержанием CO2. Первый пилотный проект показал: отраслевые партнёры значительно приблизились к своей цели.
Включённые в него отдельные шаги теперь были оптимизированы с учётом их выбросов CO2 и сопоставлены с 2019 годом. Конкретный процесс включал пробную поставку продукта из «зелёной» стали от GMH Group, разработку и логистику H+B, а также дальнейшую переработку в Sandvik для получения конечного продукта.
Целью было рассчитать значения выбросов СО2 на каждом этапе производства и логистики и сделать прозрачным влияние реализованных мер на углеродный след конечного продукта.
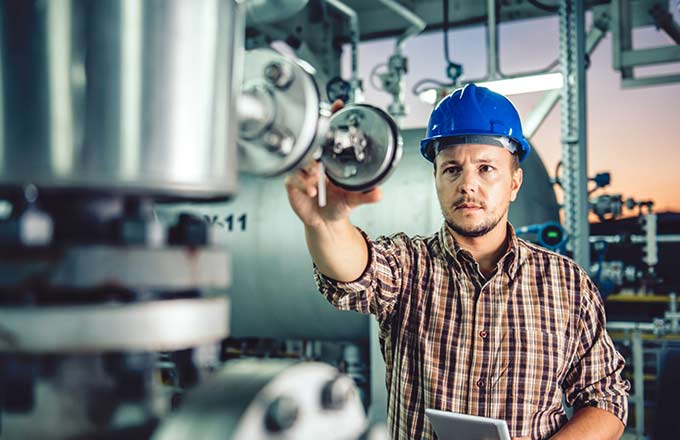
Все этапы производства конечного продукта были оптимизированы в плане сокращения выбросов углекислого газа.
Сегодня участники заявляют, что благодаря совместной работе, уменьшая выбросы на каждом этапе цепочки, они смогли в целом сократить выбросы углерода на 73%. В количественном отношении экономия составила 157 тонн CO2. Примерно сколько углекислого газа выбрасывают 60 рейсов из Франкфурта в Нью-Йорк. Как им это удалось?
По словам компании, для производства стали в GMH Group использовалась исключительно возобновляемая энергия. Заготовка для H+B была доставлена грузовиком, работающим на двигателе для сжиженного природного газа с низким содержанием CO2.
В более широком плане GMH Group стремится обеспечить дополнительную экономию диоксида углерода за счёт использования экологически чистого водорода и биогенного угля.
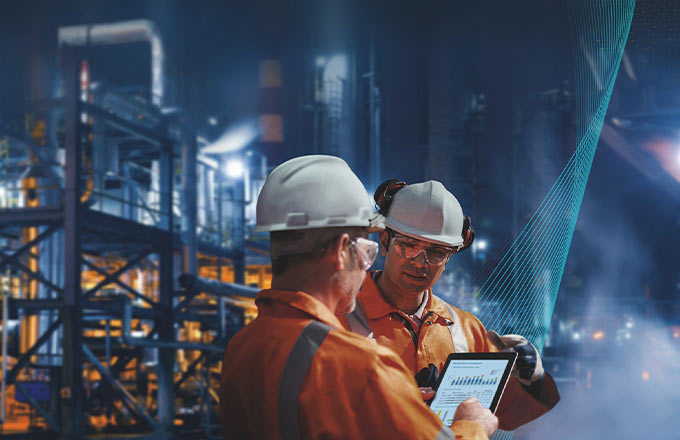
Для производства стали в GMH Group использовалась исключительно возобновляемая энергия.
В компании H+B была проведена оценка действий в области разработки и логистики. По данным торговой компании, произошёл переход на электронные погрузчики и светодиодное освещение, использование крупнотоннажных грузовиков Daimler Actros с электроприводом для пробных поставок, проекты автоматизации и оцифровки, а также установка фотоэлектрической системы для обеспечения электроснабжения.
Каждая из этих опций позволила снизить количество выбросов СО2 по отдельности, что и привело к успеху декарбонизации в целом.
В дальнейшем участники проекта собираются к 2024 году выйти на максимальный уровень экономии электроэнергии, чтобы усилить положительное влияние на углеродный баланс. Подобные примеры промышленной кооперации способны дать результат, поскольку на каждом участке этой цепочки работают профессионалы, чётко понимающие, где и как можно оптимизировать выбросы СО2 без потери качества.