Металлурги всё чаще стали внедрять на производстве RFID-метки. Radio-frequency identification в переводе с английского означает радиочастотную идентификацию. Если совсем по-русски, то это способ опознания объектов, когда радиосигналы записывают или считывают информацию, хранящуюся на RFID-метках. Ещё их называют транспондерами, которые хорошо известны водителям на платных участках дороги.
RFID относится к беспроводной системе, состоящей из двух компонентов: метки и считывателя. Считыватель — это устройство с одной или несколькими антеннами, которые излучают радиоволны и принимают сигналы обратно от RFID-метки. Где металлурги используют эту технологию и что она даёт?
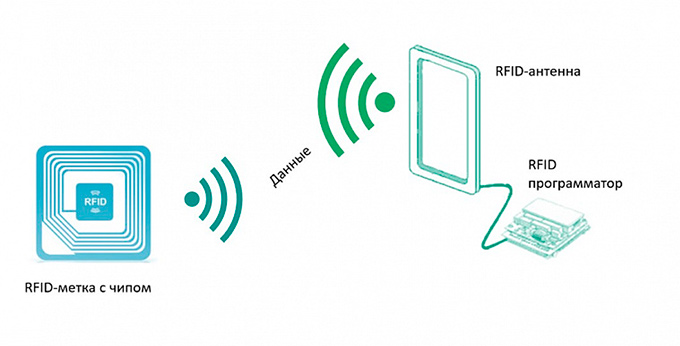
Любая RFID-метка состоит из двух основных компонентов — антенны и микрочипа
ММК
На Магнитогорском металлургическом комбинате (ММК) масштабировали RFID-решение для контроля перемещения транспорта и техники. С помощью меток металлурги теперь могут мониторить движение на участке железной дороги от доменного до электросталеплавильного цеха.
Суть метода в следующем. На пути от доменного производства вдоль железнодорожных путей установлены считыватели, а на чугуновозных ковшах появились оснащённые антенной и чипом RFID-метки. Данные от устойчивых к высоким температурам считывающих устройств, расположенных в контрольных точках, поступают в диспетчерскую. Специалисты предприятия получают всю информацию о месте нахождения состава и времени доставки жидкого чугуна в цеха для дальнейшего производственного процесса.
Впервые технологию RFID применили на комбинате в 2015 году. Тогда был организован контроль за миксеровозами, которые перевозят расплавленный чугун в кислородно-конверторный цех.
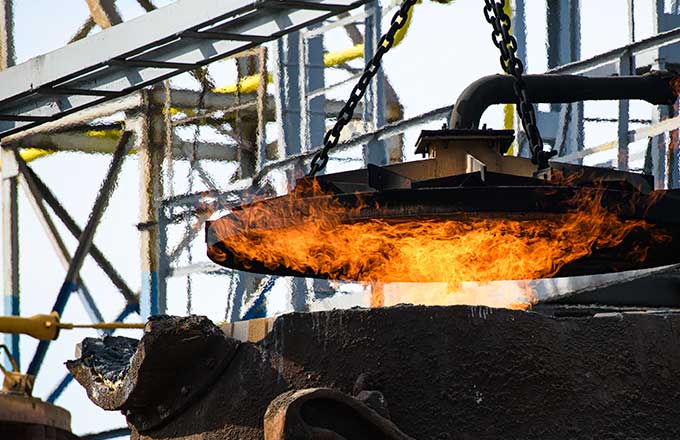
Чугуновоз перевозит жидкий чугун на территории комбината
«Единая система, объединившая доменный, электросталеплавильный и кислородно-конверторный цеха, ускорила получение информации, тем самым повысив эффективность использования транспортных средств и сократив время их простоя. Мы контролируем каждый миксеровоз и чугуновозный ковш на любом отрезке заявленного пути в реальном времени. Как результат, не допускается остывание расплава и нарушение технологического цикла, а тара своевременно подаётся под выпуск чугуна на доменной печи», — отметил инженер-технолог доменного цеха Самат Миникаев.
На Магнитке RFID-метки устанавливают не только на технику, но даже на средства индивидуальной защиты металлургов и это уже помогает решать вопросы, связанные с промышленной безопасностью. Так, на коксовых машинах специальные датчики определяют, на каком расстоянии сотрудник находится от работающего оборудования. При сближении коксовых машин с работником на радиометку, вмонтированную в каску, поступает вибросигнал. В этот же момент на коксовой машине включается световая и звуковая сигнализация и происходит блокировка её механизмов.
«Северсталь»
В «Северстали» RFID-метки размещаются на ключевых узлах оборудования и взаимодействуют с приложением «Мобильное ТОРО», установленным на терминалах сбора данных обслуживающего персонала. С помощью этих устройств сотрудники получают доступ к информации о состоянии оборудования, истории неисправностей и перечню необходимых операций, будь то аварийный ремонт или регламентное обслуживание.
Преимущества и примеры использования RFID-меток в ТОиР:
1. Сокращение времени на принятие решений. Использование RFID-меток позволяет свести к минимуму задержки в процессе ремонта, исключив длительный поиск информации об оборудовании.
Пример: В случае аварийной ситуации мастер ремонтной службы сканирует RFID-метку на неисправном оборудовании. На экране терминала автоматически отображаются данные о технических характеристиках объекта, история неисправностей, а также рекомендации по выполнению ремонта или профилактического обслуживания. Это упрощает диагностику и позволяет мастеру оперативно приступить к выполнению работ.
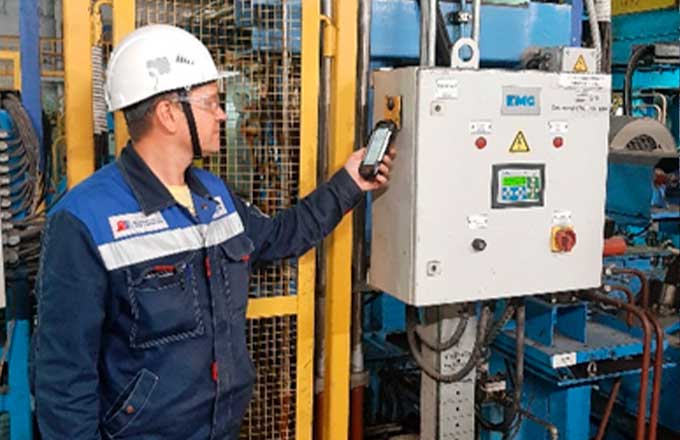
Считывание RFID-метки для идентификации оборудования и контроля персонала
2. Мониторинг взаимодействия с оборудованием. RFID-метки подтверждают факт начала работ. Сотрудник, приступая к ремонту, обязан отсканировать метку, что фиксируется системой как регистрация его взаимодействия с объектом.
Пример: Каждая единица оборудования снабжена уникальной RFID-меткой. Мастер сканирует метку с помощью терминала сбора данных перед началом работы. Это действие подтверждает его физическое присутствие рядом с объектом и фиксируется в системе. Такой подход позволяет исключить вероятность фиктивного выполнения задачи, делая ремонтный процесс прозрачным.
3. Контроль длительности обслуживания. Система отслеживает время от момента сканирования метки оборудования до завершения работ, что даёт возможность анализа эффективности и выявления возможных отклонений.
Пример: если система фиксирует, что нормативное время на выполнение ремонтной операции (например, 30 минут) было существенно сокращено (например, до 5 минут), это может стать поводом для запроса дополнительных доказательств, таких как фотографии или комментарии мастера. Такой контроль помогает не только выводить на новый уровень дисциплину сотрудников, но и проверять качество выполнения задач.
4. Подтверждение выполнения работ в суровых погодных условиях. Одной из ключевых проблем, с которой сталкивается обслуживающий персонал на предприятиях зимой, является работа в сложных погодных условиях, таких как сильные морозы, когда взаимодействие с техникой или терминалами данных становится затруднительным. В «Северстали» внедрили решение, позволяющее свести к минимуму манипуляции с терминалами сбора данных и сделать процесс удобным даже при температуре -30 °C и ниже.
Пример: в рамках системы «Мобильное ТОРО» в компании настроили функцию автоматической фиксации выполнения работ. Мастеру достаточно только приблизить терминал сбора данных к RFID-метке оборудования, чтобы система автоматически зарегистрировала его взаимодействие. После завершения работ мастер снова сканирует RFID-метку, действия завершаются без необходимости ручного ввода данных или длительного взаимодействия с экраном устройства.
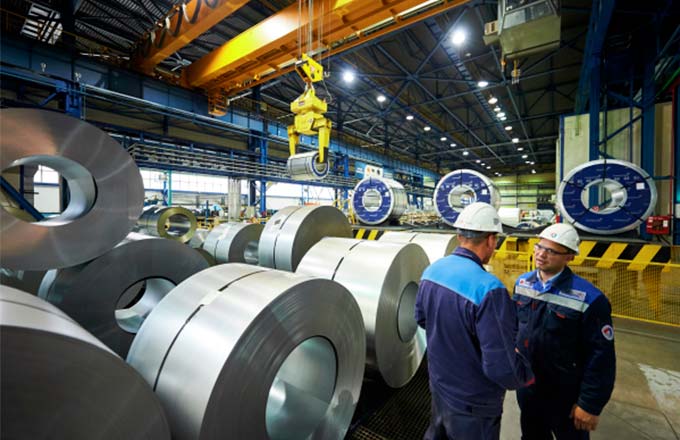
«Северсталь» — один из ведущих производителей стали в России и специализируется на листовом прокате с высокой добавленной стоимостью
Результат: Такой подход позволил упростить процесс регистрации операций и учёта времени, снизив вероятность ошибок и неудобства для сотрудников, работающих в сложных погодных условиях.
- Ключевые результаты внедрения RFID:
- Исключение затруднений при доступе к данным об оборудовании.
- Повышение ответственности ремонтного персонала за выполнение работ.
- Прозрачность всех этапов ремонта.
- Оптимизация простоя оборудования за счёт сокращения времени на диагностику и устранение неисправностей.
НЛМК
Температура чугуна из доменной печи составляет примерно 1500 °С. На пути к конвертерному цеху он охлаждается. Задача сталеваров — потерять как можно меньше градусов. Поэтому за ковшами необходимо следить на всём пути их следования, чтобы они нигде не простаивали.
Раньше на НЛМК информация о передвижении ковшей передавалась между сотрудниками по телефону или рации. Теперь для их отслеживания используются RFID-метки и платформа «DEM — Цифровая модель предприятия».
Чтобы внедрить технологию, на ключевых точках транспортировки чугуна были смонтированы шкафы с RFID-оборудованием и две RFID-антенны. В «горячих» цехах антенны оснастили защитными кожухами. К стенкам ковшей приварили RFID-метки, которые залили теплоизоляционным и жаропрочным материалом и поместили в стальные корпуса. Конструкция защищает метки от высокой температуры, механических и климатических воздействий.
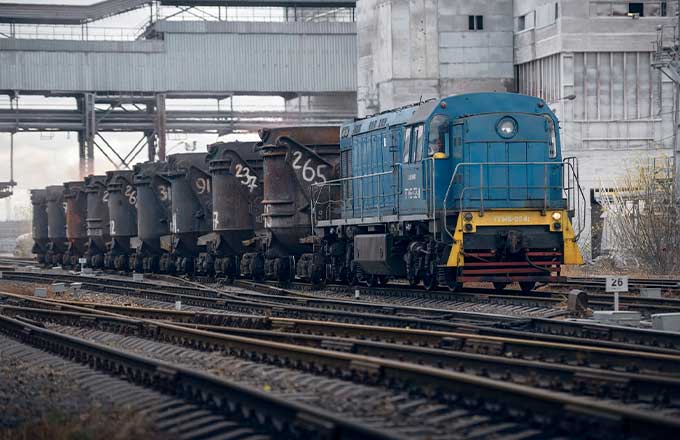
Маневровый тепловоз ТГМ6Д-0320 ведёт ковши в конвертерный цех
Чтобы технология заработала:
- Была создана цифровая копия комплекса в виде мнемосхемы;
- Точки контроля и идентификации ковшей отметили в соответствии с физическим расположением оборудования;
- Метки внесли в систему;
- Были прописаны сценарии работы во встроенном в платформу DEM редакторе;
- Были созданы учётные записи для диспетчеров.
Метка на ковше сканируется антенной на пути его транспортировки. К ней привязан уникальный ID с данными о температуре перевозимого сплава, номере выпуска, химсоставе, маршруте движения. Информация отображается в системе и на мнемосхемах. С их помощью диспетчеры всегда знают, где находится каждый ковш, и могут отследить весь его жизненный цикл.
Ключевые результаты внедрения RFID:
- Сократилось время простоя ковшей;
- Снизились теплопотери расплавленного чугуна при транспортировке;
- Возросла прозрачность процессов: теперь сотрудники точно знают статус ковшей (гружёные или нет, где находятся) и насколько хватает их ресурса;
- Легче проводить плановое техобслуживание, так как доступна история всех ковшей;
- Полная цифровизация и автоматизация операций считывания данных о бизнес-процессах;
- Есть интерфейс агрегации всех данных на удобной цифровой модели предприятия;
- Считывание идентификаторов происходит без участия человека — человеческий фактор полностью исключён;
- Может считывать сотни идентификаторов в секунду;
- Пользовательское ПО не требует установки на компьютер — это веб-интерфейс.
Егор Петров