В предыдущих материалах нашего небольшого исторического экскурса мы рассмотрели, как развивалась металлургия на заре человеческой цивилизации, в эпоху античности, какие изменения она претерпела в средневековье и насколько революционным для сталеваров стал 19-й век. Именно тогда металлургия стала основой основ для экономики и государственного развития передовых стран мира, включая и Россию, которая не только стремилась не отставать, но в каких-то аспектах сама задавала металлургические тренды.
Настало время перейти к совсем недавнему прошлому, то есть к 20 веку, в котором многие из нас родились, а некоторые даже и выросли. В этом столетии потребность в металлургической продукции продолжала расти практически в геометрической прогрессии, именно 20 веку обязаны своим рождением крупнейшие металлургические комбинаты в мире, в том числе и в Советском Союзе. Но началось всё с кораблестроения.
«Титаник»: триумф и трагедия индустриального века
К началу XX века кораблестроение достигло уровня, позволявшего создавать суда невиданного ранее масштаба. Одним из наиболее известных примеров стал крупнейший лайнер своего времени «Титаник», затонувший в первом же рейсе в 1912 году.
Для постройки гигантского судна потребовалось около 46 тысяч тонн стали. Однако металлургические технологии того времени не поспевали за амбициями судостроителей.
При столкновении с айсбергом давление, по оценкам, достигало до 2,5 тонны на квадратный сантиметр, и стальные листы выдержали удар. Однако слабым звеном оказались заклёпки, изготовленные из железа с высоким содержанием шлака и потому обладавшие повышенной хрупкостью. Под ударной нагрузкой многие из них разрушились, что привело к разрыву швов и быстрому затоплению отсеков корабля.
Крушение «Титаника» ясно продемонстрировало предел возможностей металлургических технологий XIX века и стало стимулом к поиску новых решений. Новая эпоха требовала от металлургов совершенно иного подхода к стали: более высокой устойчивости к ударным нагрузкам, надёжности в экстремальных условиях и точного контроля за качеством материалов в массовом производстве. Проследим, как шаг за шагом развивалась металлургия в XX веке и какие решения стали для неё определяющими.
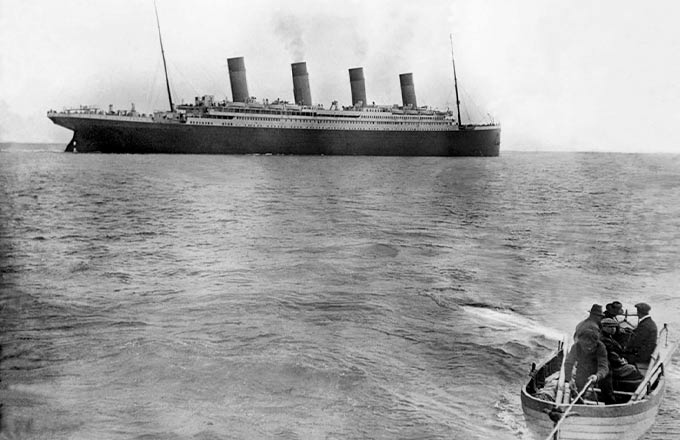
Для "Титаника" потребовалось около 46 тысяч тонн стали.
Легированные стали: от экспериментов к индустриальному прорыву
Ответом на возросшие требования новых технологий стало широкое внедрение легированных сталей. Прочность, пластичность, стойкость к коррозии и высоким температурам — каждая отрасль предъявляла свои требования, и металлургия находила на них ответы.
Идея улучшения свойств стали с помощью добавок появилась задолго до XIX века. Древние кузнецы интуитивно использовали руды с примесями, что влияло на прочность и пластичность металла. Одним из примеров природного легирования было метеоритное железо с содержанием никеля, обладавшее высокой устойчивостью к коррозии.
В первой половине XIX века русский металлург Павел Аносов заложил научную основу легирования, исследуя влияние различных примесей на структуру стали. Позднее, в 1882 году, английский металлург Роберт Гадфильд разработал первую массовую марганцовистую сталь с высокой прочностью и износостойкостью. Этот сплав применяется до сих пор в конструкциях, подверженных ударным нагрузкам.
Тем не менее, до конца века легирование оставалось преимущественно в сфере экспериментов. Лишь с развитием металловедения — новой науки о внутренней структуре металлов — стало возможным точно подбирать состав и режимы обработки под конкретные задачи.
К рубежу XIX–XX веков усилившаяся артиллерия потребовала от металлургов более прочных материалов для орудий и брони. Это привело к активному применению легирующих элементов никеля, хрома, марганца и совершенствованию термообработки с целью добиться сочетания твёрдой поверхности и вязкой сердцевины.
Первым масштабным примером такого подхода стала броня, разработанная компанией Krupp в 1893 году. Она сочетала цементацию и легирование хромом, быстро стала стандартом для флота и широко использовалась в Первую мировую войну.
Так легированные стали вышли за рамки экспериментов и стали основой конструкций в артиллерии, бронетехнике и машиностроении. В полной мере их потенциал раскрылся в бронетехнике — особенно в танках, где защита экипажа стала одной из сложнейших задач для металлургов.
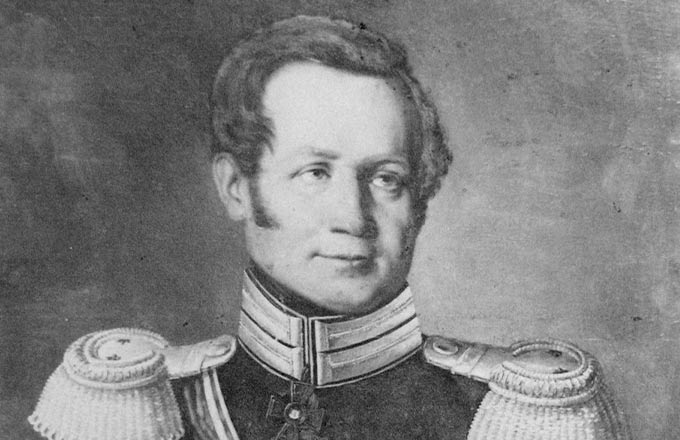
Русский металлург и учёный Павел Аносов.
От броневой стали к композиту: как развивалась танковая защита
С момента превращения танков в ключевое средство сухопутных операций основной задачей бронезащиты стало обеспечение сохранности экипажа и критически важных узлов машины при воздействии артиллерийского огня, кинетических и кумулятивных боеприпасов. При этом защита должна была быть прочной, технологичной и не делать машину слишком тяжёлой для манёвра.
Каждое новое поколение боеприпасов повышало требования к броне, защита развивалась в постоянной гонке с наступательными технологиями.
Гомогенная броня
Во Второй мировой войне основным типом защиты оставалась гомогенная броня — однородная сталь, одинаковая по структуре и составу на всей толщине плиты. Такие стали обеспечивали высокую прочность, хорошую свариваемость и предсказуемость при ударном воздействии.
Примеры:
• Т-34 (СССР): корпус и башня из катаной гомогенной брони на основе стали марки 8С с добавками марганца, хрома и никеля.
• Panther, Tiger I (Германия): применялись как литые, так и катаные гомогенные броневые плиты, с использованием никеля, хрома и молибдена.
Гомогенная броня применялась в серийных танках до 1960-х годов и в отдельных элементах продолжает использоваться по сей день.
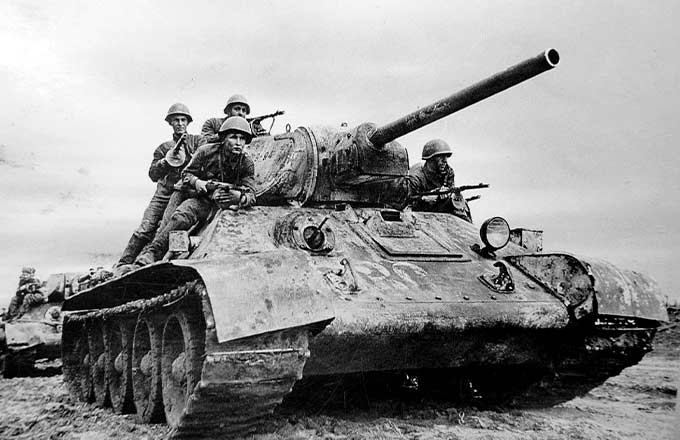
Легендарный Т-34.
Термическая обработка
Следующий этап развития касался не конструкции брони, а улучшения свойств уже применяемых сталей. Упрочнение броневых сталей достигалось за счёт методов термообработки — закалки, нормализации и отпуска, которые позволяют повышать твёрдость внешнего слоя при сохранении необходимой вязкости и пластичности.
Пример: На Т-34 применялась закалка лобовой брони, особенно на участках со скосами, наиболее подверженных ударной нагрузке.
Многослойная броня
С начала 1960-х годов начался переход к многослойным конструкциям брони. Это был первый шаг к принципиальному изменению архитектуры защиты: теперь различные по свойствам металлические материалы — сталь, алюминий и другие — начали сочетаться в едином броневом пакете.
Пример: Т-64 (СССР): первый в мире серийный танк с многослойной бронёй. Конструкция включала внешние слои из стали и внутренний алюминиевый наполнитель с ячеистой структурой. Такое сочетание обеспечивало повышенную защиту как от кинетических, так и от кумулятивных боеприпасов.
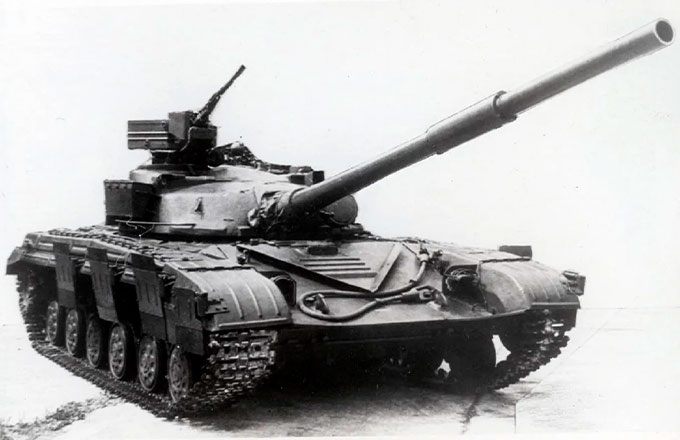
Танк Т-64 до сих пор находится на вооружении многих армий мира.
Современные методы металлургии
Для того чтобы реализовать всё более сложные требования к броне — как многослойной, так и последующей композитной, потребовалось совершенствовать саму металлургическую базу. В послевоенное время начали активно внедряться вакуумная плавка и электрошлаковый переплав. Эти методы позволили получать броневые стали с высокой чистотой и однородностью, снизить уровень вредных включений и повысить надёжность при динамических нагрузках.
Композитная броня
Со временем одних только свойств стали стало недостаточно — акцент сместился с материала на конструкцию. Началась эпоха композитной брони, где сталь стала лишь частью более сложной системы.
В таких броневых пакетах сочетаются металл и неметаллы — керамика, стеклотекстолит, полимерные связующие. В отличие от многослойной защиты с преимущественно металлическими слоями, композиты позволили точнее управлять физическими свойствами брони.
Примеры:
• Т-80У, Т-90 (СССР/Россия): композитная броня с металлическими и керамическими элементами.
• M1 Abrams (США): броня типа Chobham — сталь и керамика.
• Leopard 2A5/2A7 (Германия): модульные композитные блоки с металлическими и неметаллическими вставками.
Примечание: керамика, благодаря твёрдости и малой плотности, эффективно разрушает сердечники снарядов, повышая защиту без значительного увеличения массы.
Таким образом, гомогенные стали легли в основу танковой брони в первой половине XX века. По мере усиления вооружения и повышения требований к подвижности машин броня усложнялась: сначала за счёт термической обработки и улучшения состава, затем — через переход к многослойным и композитным конструкциям.
При всей сложности современных решений сталь остаётся несущим каркасом бронезащиты, а эффективность конструкции определяется не столько толщиной, сколько точным подбором и сочетанием материалов.
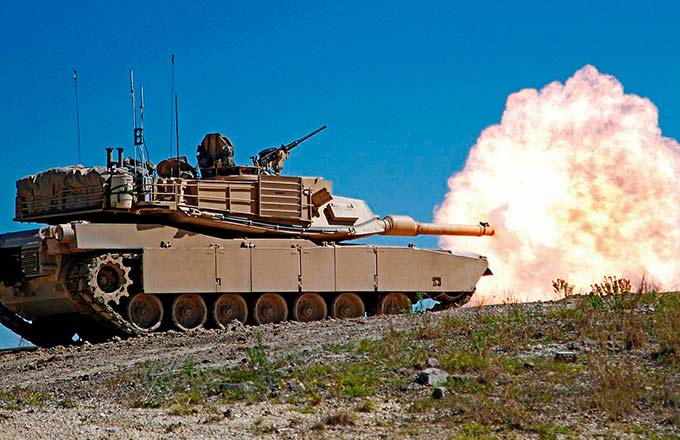
Американский "Абрамс".
Сталь — испытание высокими нагрузками и температурами
Развитие броневой защиты — лишь один из примеров того, как металлурги расширяли пределы возможностей стали, отвечая на всё более жёсткие требования. То же самое происходило в других отраслях — авиации, энергетике, ракетостроении и атомной промышленности. Везде, где возрастали температуры, давления и силовые нагрузки, сталь оставалась основой конструкции, но только при условии постоянного совершенствования состава и методов обработки.
В авиации высокопрочные легированные стали по-прежнему применяются в ответственных узлах: в каркасах фюзеляжа, шасси, соединительных элементах и ряде компонентов двигателей. Такие стали выдерживают большие механические и вибрационные нагрузки, а также повышенные температуры. Характерный пример — советский перехватчик МиГ-25, около 80% конструкции которого было выполнено из жаропрочной нержавеющей стали.
Это позволило самолёту выдерживать нагрев корпуса при полётах на скоростях свыше трёх скоростей звука.
Однако с ростом требований в ряде направлений сталь начала приближаться к пределу своих характеристик:
• Авиационные двигатели. Температура газа перед турбиной достигает 1300 °C и выше. Сталь используется в конструктивных частях, но в зоне непосредственного теплового воздействия её заменяют жаропрочные никелевые сплавы.
• Ракетные двигатели. В камере сгорания температура превышает 3000 °C, давление — до 20–30 МПа. Даже с активным охлаждением стенки сопла нагреваются до 700–800 °C. В таких условиях сталь применима лишь в трубопроводах, корпусах турбонасосов и других вспомогательных элементах.
• Энергетика. В современных ТЭС паровые турбины работают при температуре 550–600 °C и давлении до 25 МПа. Здесь сталь сохраняет свои позиции, особенно при использовании жаропрочных марок и контролируемой термической обработки.
• Атомная энергетика. Корпуса реакторов, парогенераторы и оболочки топлива работают под воздействием высоких температур, давления и нейтронного излучения. Здесь применяются специальные радиационно-стойкие марки стали, такие как ферритно-мартенситные и аустенитные.
Во всех этих сферах металлурги шаг за шагом повышали пределы применимости стали — через легирование, вакуумную металлургию, электрошлаковый переплав.
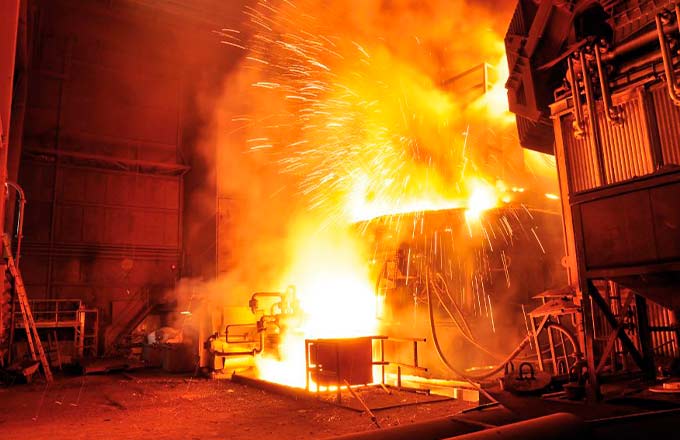
Устойчивость к высоким температурам - один из главных вызовов для современных металлургов.
Как XX век изменил производство стали
Мартеновские печи долго оставались основой сталеплавильного производства, но для легирования они были менее пригодны: температурный режим был нестабилен, а потери легирующих элементов высоки.
Однако в годы войны на Урале, в Магнитогорске, была разработана и применена технология выплавки броневой стали в больших мартеновских печах, что позволило значительно увеличить объёмы её производства, крайне необходимые для нужд фронта.
С начала XX века начали активно внедряться электродуговые печи, обеспечивавшие точное управление плавкой и составом. Это открыло возможности для производства легированных сталей с заданными свойствами.
В середине века началась разработка вакуумной обработки, что позволило удалять газы и повышать чистоту стали. Примерно в то же время появился электрошлаковый переплав (ЭШП), который получил широкое распространение в СССР и некоторых европейских странах. Однако на Западе чаще применялись вакуумно-дуговая плавка и другие энергоэффективные технологии, что ограничило применение ЭШП.
Параллельно развивался кислородно-конвертерный процесс, менее точный, но гораздо более эффективный метод массового производства стали для нужд строительства, транспорта и тяжёлой промышленности.
XX век стал испытанием на прочность и для самих сталеваров, которые упорно, шаг за шагом, расширяли пределы возможностей металла.
Под давлением сверхскоростей, высоких температур и радикально новых вооружений сталь непрерывно совершенствовалась, оставаясь основой современной цивилизации.
И хотя в отдельных сферах сталь достигла естественных ограничений, открывая дорогу новым высокотехнологичным материалам, она по-прежнему незаменима и продолжает развиваться, отвечая на вызовы XXI века.
Вадим Чепига