Неожиданный эффект вызвал доклад Юрия Бороненко, заведующего кафедрой «Вагоны и вагонное хозяйство» в ФГБОУ ВО «Петербургский государственный университет путей сообщения Императора Александра I» на ХVIII Международной научно-технической конференции «Подвижной состав XXI века: идеи, требования, проекты».
На сессии эксперт обратился к теме современных алюминиевых сплавов и их применения в вагоностроении. У некоторых наблюдателей после выступления профессора сложилось впечатление, что вагоны из алюминиевых сплавов не могут попасть на железную дорогу из-за несовершенства нормативной базы, нехватки данных относительно выносливости конструкций из алюминия и… необходимости красить вагоны. Как представляется, для такой трактовки нет оснований.
На какой конференции выступил Юрий Бороненко?
ХVIII Международная научно-техническая конференция «Подвижной состав XXI века:идеи, требования, проекты» состоялась 9-12 июля 2024 года в Санкт-Петербурге. Форум был организован Петербургским государственным университетом путей сообщения Императора Александра I при поддержке Научно-исследовательской лаборатории «Динамика вагонов», Научно-внедренческого центра «Вагоны», Союза «Объединение вагоностроителей», компании «РМ Рейл», Всесоюзного научно-исследовательского центра транспортных технологий.
Стандарты в норме
В реальности Юрий Павлович Бороненко говорил о текущем состоянии дел в производстве подвижного состава с конструкциями из алюминиевых сплавов и тех задачах, которые естественным образом возникают по мере развития алюминиевого тренда в вагоностроении.
Начнём с того, что алюминиевые грузовые вагоны в России производят и эксплуатируют уже семь лет: в январе 2017 года сертифицировали первый хоппер-минераловоз из сплава 1565ч модели 19-1244, созданный компанией «РМ Рейл» и Самарским металлургическим заводом. С тех пор отечественные предприятия выпускают хопперы-минераловозы из сплава 1581, вагоны-цистерны из сплава 1407ч и контейнер-цистерны для перевозки сжиженного природного газа из сплава 1581.
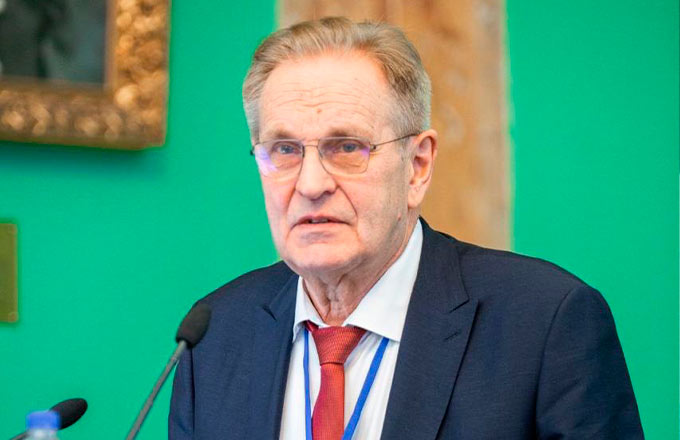
Юрий Бороненко, заведующий кафедрой «Вагоны и вагонное хозяйство» в ФГБОУ ВО «Петербургский государственный университет путей сообщения Императора Александра I»
Внедрению алюминия в вагоностроение само собой сопутствуют развитие и актуализация нормативной базы. В 2022 году вступили в силу сразу два профильных документа: ГОСТ Р 59598-2021 «Алюминий и алюминиевые сплавы. Полуфабрикаты для производства элементов кузовов грузового подвижного состава железнодорожного транспорта.
Технические условия и сортамент» и ГОСТ Р 59849-2021 «Соединения сварные конструкций кузовов железнодорожного подвижного состава из алюминиевых сплавов». «Про Металл» не так давно рассказывал об этом довольно подробно. Добавим только, что в 2023 году Росстандарт также утвердил изменение в ГОСТ 4784-2019 «Алюминий и сплавы алюминиевые деформируемые. Марки», включив в стандарт 11 сплавов, в том числе упомянутые уже сплавы 1581 и 1407ч.
В работе над перечисленными стандартами участвовали все стейкхолдеры. Это 35 организаций из состава Технического комитета 045 «Железнодорожный транспорт» и НП «ОПЖТ», в том числе АО «ВНИКТИ», ООО «ВНИЦТТ», ОАО «РЖД», «РМРейл», Союз «Объединение вагоностроителей», ПАО «НПК Объединённая вагонная компания» и, конечно, Алюминиевая ассоциация.
Таким образом, о каких бы то ни было недостатках нормативной базы в части применения алюминия в вагоностроении говорить не приходится.
Уроки физики и механики
Другое дело, что, как отметил в докладе Юрий Бороненко, в существующей нормативной документации нет данных о выносливости алюминия при воздействии динамических нагрузок. Но это поправимо, тем более профессор тесно связан с практиками-вагоностроителями и является автором методики определения технического уровня разрабатываемого железнодорожного подвижного состава, применяемой для формирования и актуализации соответствующей нормативной базы.
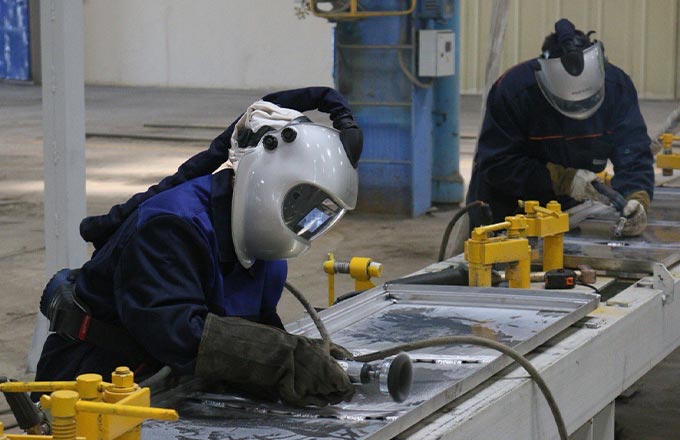
Профессор Бороненко тесно связан с практиками-вагоностроителями и является автором методики определения технического уровня разрабатываемого железнодорожного подвижного состава.
Впрочем, по словам Юрия Бороненко, принципиальных отличий в методике проектирования алюминиевых несущих конструкций нет. «Расчёт несущих конструкций из алюминиевых сплавов аналогичен расчёту конструкций из стали, но алюминиевые сплавы имеют отличные физические и механические свойства», — напомнил эксперт.
Это важная оговорка, ведь модуль упругости алюминиевых сплавов равен 70ГПа, что почти в три раза меньше, чем у стали. Этот показатель влияет на прогибы и устойчивость всей конструкции. Так что, конечно, в проектировании изделий из алюминия и стали есть различия.
К следующему тезису профессора — о прочности вагонов из алюминия — есть не возражение, но комментарий.Юрий Павлович справедливо заметил, что при расчётах на прочность подвижного состава обычно используется показатель предела текучести с некоторым коэффициентом запаса.
Прочность вагона из алюминия ниже, чем у стального. Из-за этого, например, алюминиевые полувагоны не разгружают экскаваторами, т.к. ковш ненароком может задеть и деформировать кузов вагона. Эксплуатанты нашли решение в виде специальных опрокидывателей.
А на производстве для компенсации недостатка прочности, как и сказал Юрий Бороненко, увеличивают площадь и момент инерции несущих конструкций из алюминиевого сплава. «С точки зрения удельной прочности по пределу текучести можно ожидать снижение массы конструкции с использованием алюминиевых сплавов в 1,5–1,7 раза», — подчеркнул профессор.
К слову, «Про Металл» уже приводил данные, озвученные Юрием Бороненко на форуме «Подвижной состав: производство, эксплуатация и ремонт». Эксперт сообщил, что удельная прочность алюминиевого сплава в три раза выше, чем у низколегированной стали. Не подвергая сомнению сказанное, можно лишь упомянуть, что есть современные алюминиевые сплавы, которые по показателю предела текучести близки к сталям.
А вот следующее утверждение докладчика требует уточнения. Он посетовал на недостаток данных о выносливости алюминиевых изделий, применяемых в вагоностроении. Выносливость, напомним, представляет собой важнейший для проектировщика вагонов показатель — зависимость между величинами средних напряжений и числами циклов до разрушения.
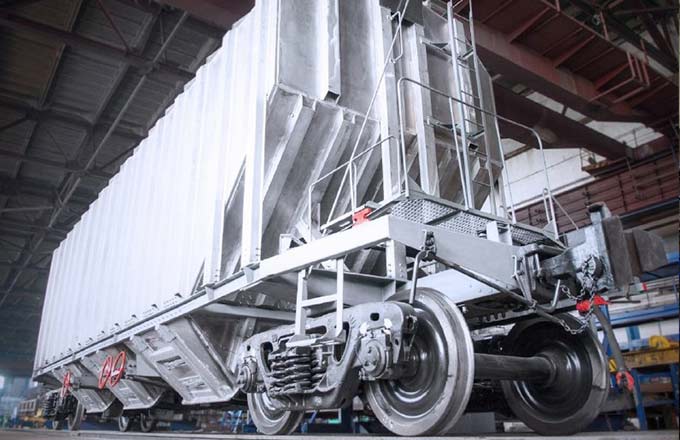
Прочность вагона из алюминия ниже, чем у стального. Из-за этого, например, алюминиевые полувагоны не разгружают экскаваторами.
Между тем показатели сопротивления усталости практически всех алюминиевых сплавов известны. За ними можно обратиться в московский Институт лёгких материалов и технологий (ИЛМиТ). Правда, в дискуссиях о характеристиках выносливости алюминиевых сплавов обычно используют другие аргументы.
Так, в отличие от стали, у алюминия по большому счёту нет понятия предела выносливости, и если у стали на графике характерная прямая в области высоких циклов, то у алюминия кривая постоянно устремляется вниз. Это зачастую смущает проектировщиков. Но все недостающие данные можно получить через испытания на длительных циклах.
Сваренные вкрутую
Отдельно Юрий Бороненко остановился на сварных швах в вагонах из алюминия. Напомним, для соединения алюминиевых элементов конструкции вагонов наряду с аргонно-дуговой сваркой используется хорошо зарекомендовавшая себя технология сварки трением с перемешиванием. Этот метод обеспечивает высокую скорость соединения листов металла — до одного метра в минуту.
Докладчик обратил внимание на наличие существенной разницы в расчётах по ГОСТ 33211-2014 «Вагоны грузовые. Требования к прочности и динамическим качествам» и «Нормам», которыми пользуются вагоностроители. По мнению эксперта, следует отказаться от упрощённого способа определения предела выносливости сварных соединений алюминиевых сплавов. Заметим, что ГОСТ 33211-2014 в настоящем своём виде не связан с алюминием, в то время как в ГОСТ Р 59849-2021 данные о пределе выносливости и усталостных характеристиках металла представлены ясно и подробно.
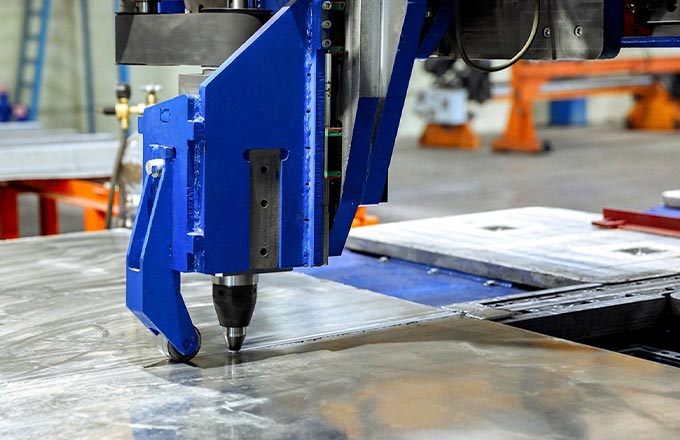
У алюминия по большому счёту нет понятия предела выносливости, что доказано многочисленными лабораторными испытаниями.
По мнению Юрия Бороненко, нужно путём эксперимента определить показатели усталостной прочности сварных соединений для различных их видов. Необходимо наметить общую программу испытаний, на основе которых можно будет создать справочную базу показателей ограниченного предела выносливости сварных соединений алюминиевых сплавов.
Действительно, испытания конкретных типов сварных соединений алюминия ещё не проводились. Впрочем, возможноэто актуально и для сталей, применяемых в вагоностроении.
В натуральном цвете
Ещё один аспект алюминиевого вагоностроения, затронутый Юрием Бороненко, на первый взгляд может показаться курьёзом. Но если разобраться, на самом деле все серьёзно. Судите сами. Согласно нормативной документации, кузова вагонов и подвагонное оборудование должны быть окрашены масляными красками или эмалями.
Между тем одно из неоспоримых достоинств алюминиевых вагонов заключается в том, что их не нужно красить — от коррозии металл и так защищён естественной оксидной плёнкой. К тому же алюминий не взаимодействует с активными средами, такими, например, как калийные удобрения. Этот металл также стоек к щелочной и кислотной среде.
Как замечает Юрий Бороненко, выполнение требований по окрашиванию алюминиевых вагонов неизбежно ведёт к дополнительным расходам при производстве и обслуживании подвижного состава. А значит, практику обязательного нанесения краски на вагоны следует оставить в прошлом, включив для этого в ГОСТы необходимые изменения.
Но тут и карты в руки экспертам из Петербургского государственного университета путей сообщения Императора Александра I и вагоностроительных предприятий, которые активнейшим образом участвуют в разработке стандартов на технику железных дорог.
Коррозия, на выход!
Говоря о решении технических задач на практическом уровне, Юрий Бороненко привёл в пример способ, к которому прибегли разработчики первого алюминиевого вагона-хоппера модели 19-1244 для предотвращения гальванической коррозии. В конструкции вагона нельзя было допустить непосредственного контакта алюминиевых и стальных деталей из-за их разной электрохимической активности. Конструкторы использовали специальные прокладки, и потенциальная проблема была снята. Опытная эксплуатация более чем двух сотен вагонов-хопперов из первой партии не выявила коррозионных повреждений подвижного состава.
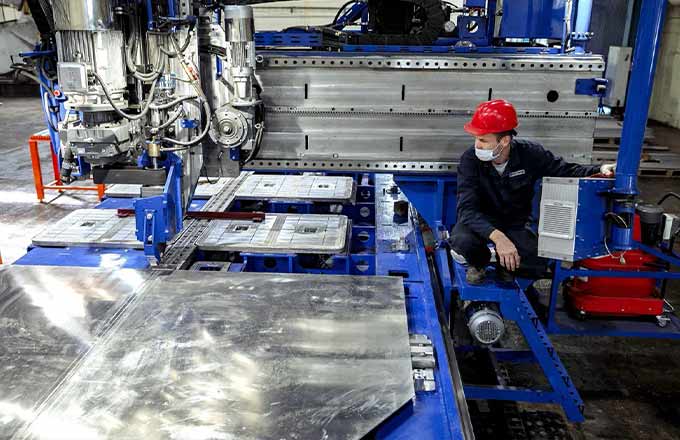
Практику обязательного нанесения краски на вагоны следует оставить в прошлом, включив для этого в ГОСТы необходимые изменения.
В востребованности алюминиевого подвижного состава ни у кого из участников рынка нет сомнений. Операторы и грузоотправители получают выгоду от снижения массы тары, увеличения грузоподъёмности и срока службы вагонов. Владелец железнодорожной инфраструктуры получает увеличенную провозную способность железных дорог и снижение затрат на их содержание. А вагоностроители видят среди потенциальных покупателей алюминиевых вагонов не только отечественных, но и зарубежных железнодорожных операторов.
Когда же на пути внедрения алюминиевых решений возникают какие-либо новые вызовы, накопленных в отечественном вагоностроении компетенций оказывается достаточно для ответа на них. Об этом, собственно, и рассказал Юрий Бороненко в своём докладе на конференции.
Пётр Орлов