Искусственный интеллект (ИИ) в связке с роботизированными механизмами распространяются по всем сферам промышленности, теперь они добрались и до управления тяжёлыми отраслями. Сталевары одними из первых в металлургии взяли на службу ИИ и их совместные проекты позволяют избежать простоев на предприятиях, оптимизировать расходы дорогостоящих материалов и экономить таким образом десятки миллионов рублей. Как машинное зрение, искусственный интеллект и нейросети помогают сталеварам, «Про Металл» покажет на двух уже эффективно работающих в «Северстали» и НЛМК проектах.
«Автотемп 2.0»: прокатка без пауз
Три месяца назад в «Северстали» внедрили программный комплекс по управлению темпом прокатки и выдачей слябов из печей на основе моделей машинного обучения. Решение, получившее название «Автотемп 2.0», запустили на стане 2000 Череповецкого металлургического комбината — это ключевой актив компании.
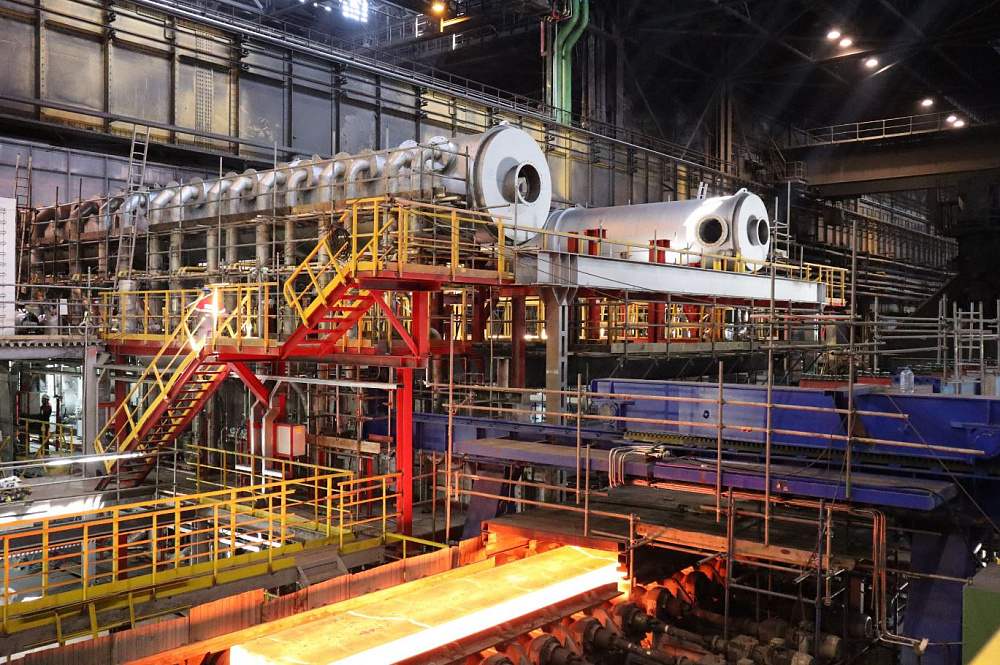
Нагревательная печь на стане 2000
Главная задача системы — рассчитать и настроить оптимальную паузу перед выдачей слябов из нагревательной печи стана и тем самым увеличить его производительность. «Автотемп 2.0» заменяет человека, проводя сложные расчёты в очень сжатые сроки. Раньше оператор самостоятельно вычислял необходимое время извлечения сляба, из-за чего могли возникать паузы в прокатке. Кроме того, решение интегрировано с моделью нагрева металла, а это улучшает параметры энергоэффективности участка нагревательных печей и качество нагрева сляба.
В чём суть системы? В основе комплекса «Автотемп 2.0» лежит модель с использованием алгоритма градиентного бустинга, который позволяет анализировать табличные неоднородные данные и с высокой точностью вычислять время прокатки металла в стане.
За три месяца работы решения экономия времени прокатки за счёт оптимизации пауз составила 27 часов, что позволило дополнительно произвести 24 тысячи тонн металлопроката.
«„Автотемп 2.0“ — это собственная разработка «Северстали», в создании которой использовались современные технологии и средства построения цифровых решений. Они позволяют развивать продукт в будущем и не зависеть от иностранных поставщиков программного обеспечения или комплектующих. Решение полностью управляет выдачей сляба, за счёт чего мы исключаем человеческий фактор и снижаем вероятность простоев агрегата. Кроме того, на участке нагревательных печей мы внедряем цифровой двойник, чтобы на основе его прогноза определять, какую из имеющихся печей лучше загрузить в определённый момент для наилучшей производительности стана 2000», — прокомментировал генеральный директор дивизиона «Северсталь Российская сталь» и ресурсных активов Евгений Виноградов.
SVS-решётка: звук в картинке
На «ВИЗ-Стали» (входит в Группу НЛМК) осенью прошлого года внедрили технологию предиктивной диагностики термического оборудования. Она позволяет оценивать состояние механических узлов и подшипников в реальном времени, заблаговременно устранять неисправности и минимизировать риски внеплановых простоев.
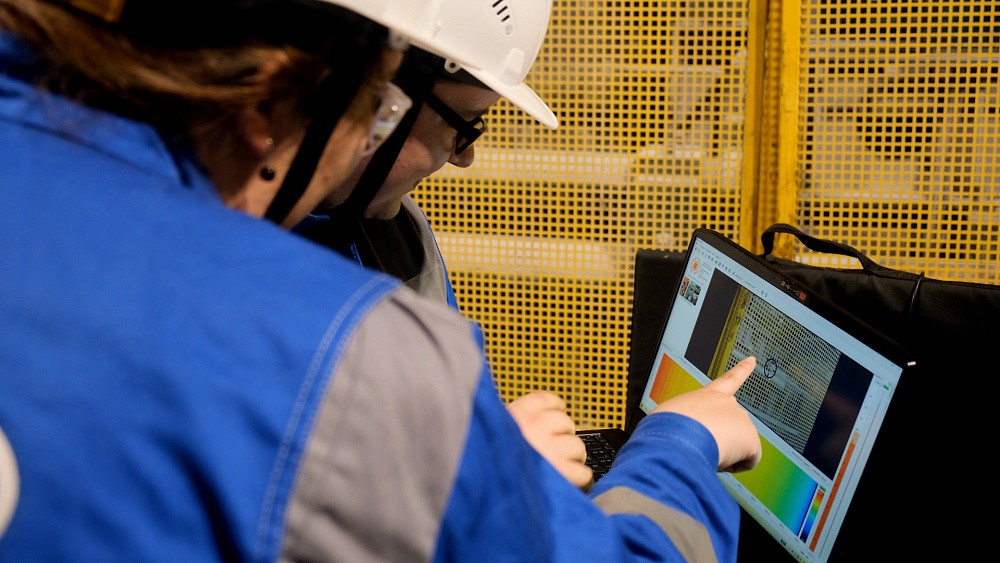
Программное обеспечение переводит звук в картинку и сравнивает с эталонной, записанной на исправном агрегате
Диагностику производят с помощью цифровой системы визуализации звука — SVS (sound visualization system). Специальная решётка с микрофонами и видеокамерой улавливает звуковые вибрации в механических частях агрегатов, свойственные процессам деформации или их началу, после чего производит видеофиксацию проблемного узла.
Программное обеспечение переводит звук в картинку и сравнивает с эталонной, записанной на исправном агрегате. Отклонения от идеала позволяют спрогнозировать поломку и своевременно провести планово-предупредительный ремонт.
По словам специалистов «ВИЗ-Стали», благодаря новой системе количество внеплановых простоев термического оборудования, которое обследуется с помощью решётки SVS, снизилось до минимальных значений. При этом сократилось время на проведение ремонтов и количество задействованного в них персонала.
В компании также планируется автоматизировать предиктивную диагностику с помощью специального робота. Тестовые испытания показали, что это позволит расширить период проведения работ и повысить точность замеров за счёт исключения человеческого фактора.
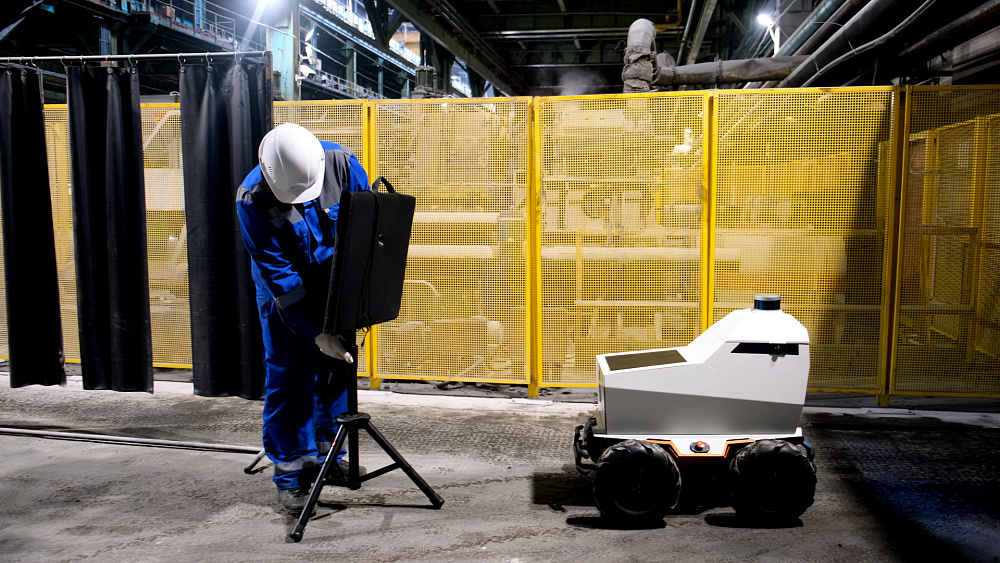
Тестовые испытания робота, который автоматизирует предиктивную диагностику
Что дальше?
Сталевары сейчас активно внедряют новейшие разработки с использованием искусственного интеллекта и нейросетей для обработки больших массивов технологических данных, контроля качества продукции на всех этапах производства. ИИ может применяться практически везде: от прокатки и термической обработки трансформаторного проката до нанесения покрытий и финишной обработки и даже до логистики. Какие выгоды получают металлурги от работы с ИИ:
- Снижаются энергозатраты. Выплавка стали — энергоёмкое производство, затраты на него зависят, например, от соотношения смеси газа и воздуха, которые подаются в топку котлов. Искусственный интеллект способен рассчитать оптимальные пропорции, в результате чего компания экономит миллионы рублей.
- Уменьшается количество брака. Чтобы в металле не возникали дефекты, важно соблюдать технологические условия. Модель обучают выявлять диапазоны режимов, которые могут привести к браку.
- Повышается качество металлопроката. Машинное обучение может определить, по какой причине на стали образуются царапины при прокате.
И всё же признаем, что металлургическая промышленность отстаёт от других секторов в применении возможностей искусственного интеллекта. Например, в химии ИИ уже сам синтезирует новые вещества. На сегодня благодаря компьютерным моделям учёные спрогнозировали существование около 150 тысяч материалов, на которые металлургам стоит обратить внимание.
По мере развития инноваций в отрасли «умные» самообучающиеся технологии играют в ней всё большую роль. Металлургические компании должны определить для себя, каким образом ИИ может принести наибольшую пользу их бизнесу. Те, кто этого не сделает, останутся позади и в ближайшие годы могут столкнуться с гонкой, в которой им не суждено победить — и именно отставание в технологиях, а не санкции, могут затормозить сталеваров.
Егор Петров