За 3D-печатью будущее, так говорят во всём мире. По данным Research and Markets, объём мирового рынка аддитивных технологий (АТ), то есть 3D-печати, к 2030-му может увеличиться в несколько раз до $83,6 млрд. Ежегодный прирост рынка — 21,2%.
В России также не отстают. С учётом тотального импортозамещения этот инструмент становится альтернативой производству оригинальных деталей. Компании занялись реверс-инжинирингом — исследованием и сканированием деталей и компонентов в целях создания аналогов. Вот только скопировать не всегда получается из-за того, что материалы пока не позволяют добиться нужной прочности. В целом надёжность напечатанных изделий, за редким исключением, заметно уступает изделиям из тех же или близких материалов, но полученных традиционными методами.
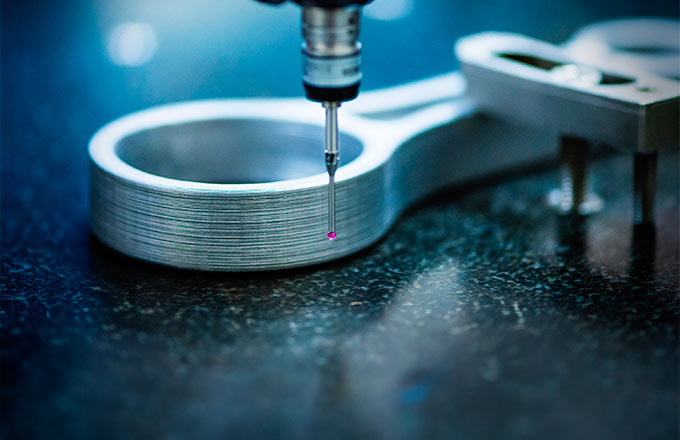
Российский рынок оборудования и услуг 3D-печати за последние несколько лет вырос в разы
Металлурги как никто заинтересован в том, чтобы их металлы использовались в 3D-печати, а изделия, вышедшие со станка, не уступали оригинальным. Произвести нестандартную деталь для испытаний всегда удобнее по технологии 3D-печати. Далее можно оптимизировать её или изменить геометрию в соответствии с требованиями конкретного заказчика.
Есть ещё один фактор, сдерживающий это направление: не хватает металлических порошков отечественных сплавов. Только в прошлом году действующему российскому парку установок аддитивного производства требовалось около 20 тонн порошков. Импортное же сырьё дорогое, а иногда и недоступное из-за санкций.
Поэтому новость о том, что «Русал» разработал новый алюминиевый сплав для 3D-печати, вызвала такой позитив. Это инновационный порошковый сплав, который предназначен для изготовления изделий с использованием технологий лазерного сплавления. Новый материал может быть использован в изготовлении двигателей, оборудования для нефтехимической отрасли, где детали подвергаются длительному нагреву, а также в силовых энергетических установках.
Испытания показали, что сплав сохраняет высокие показатели прочности до температуры 350 °С и выше, что ранее было недоступно для традиционно используемых при печати сплавов.
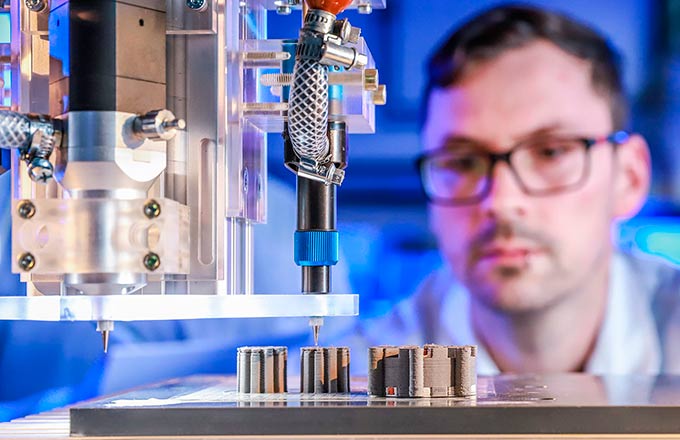
История аддитивного производства началась с изобретения первого 3D-принтера. Его сконструировал Чарльз Халл в 1983 году
Работа по созданию нового алюминиевого сплава была проведена специалистами Института лёгких материалов и технологий (ИЛМиТ). За счёт использования современных подходов моделирования фазового состава, разработчикам ИЛМиТ удалось подобрать оптимальные соотношения легирующих элементов, которые имели ограниченное использование в традиционных металлургических технологиях. С учётом низкой плотности характерной для алюминия данный материал может составить конкуренцию другим конструкционным материалам.
В других компаниях тоже есть чем похвастаться. В «Норникеле» с помощью аддитивных технологий заместили в производстве ряд деталей импортного производства — например, крейцкопф (или ползун — деталь кривошипно-ползунного механизма, совершающая возвратно-поступательное движение по неподвижным направляющим) немецкого насоса, участвующего в перекачке никелево-медного концентрата из обогатительной фабрики на металлургический завод.
Кроме того, АТ помогают повысить технологическую безопасность предприятий. С помощью 3D-печати можно самостоятельно и оперативно производить детали для ключевого оборудования, что снижает риск простоя производства.
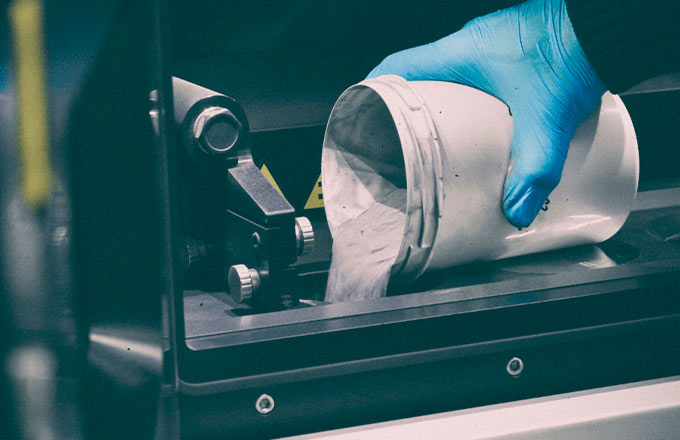
Современные технологии позволяют получить порошок для 3D-печати металлом с определёнными свойствами для решения конкретных производственных задач
На НЛМК начали использовать АТ в 2018 году. За несколько лет компания освоила производство литейных форм более чем для 100 видов разных изделий, а общее количество изготовленных с помощью АТ деталей приближается к тысяче. Среди мелких отливок можно выделить шнеки — детали с винтовой поверхностью и сложной геометрией, которые необходимы в оборудовании для изготовления металлургических брикетов. Их масса — от 9 до 120 кг. Крупные изделия в среднем весят от полутора до двух тонн, но есть экспонаты и тяжелее, до 10 тонн.
В «Северстали» освоили изготовление форсунок, плунжеров, сопел и др. На 3D-принтере производят детали из металлического порошка по технологии по SLM.
«Некоторые детали, которые мы производим на нашем принтере, стали в 10 раз дешевле, чем покупка у иностранного поставщика. Кроме этого, технология 3D-печати позволяет воспроизвести идентичные технические характеристики, а в некоторых случаях что-то добавить и улучшить. Благодаря этой технологи, мы избавились от зависимости большой цепи поставок и сроки доставки деталей сократились в разы. На данный момент мы планируем заменить иностранные детали на линиях охлаждения металла ЧерМК на детали собственного производства. Также мы ведём активную работу с компаниями «Севергрупп» в рамках импортозамещения, замены деталей с составе оборудования и научно-исследовательских работ», — отмечает директор по ремонтам дивизиона «Северсталь Российская сталь» и ресурсных активов Сергей Добродей.
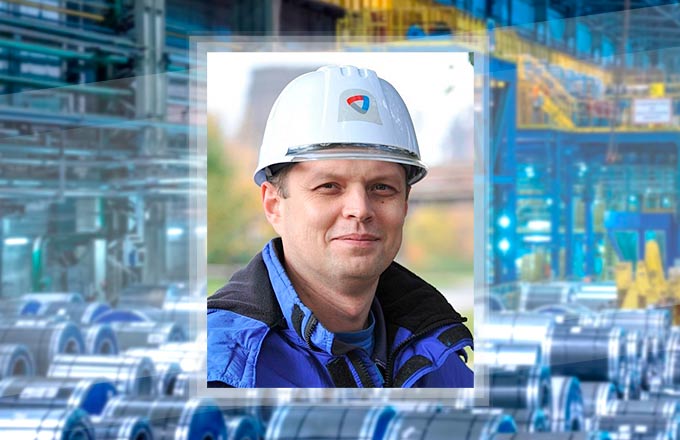
Директор по ремонтам дивизиона «Северсталь Российская сталь» и ресурсных активов Сергей Добродей
С помощью нового принтера череповецкие металлурги регулируют свойства будущего изделия. Выбирают технологии печати, материал или сплав, а также конструкцию детали. Ее задают в специализированном программном обеспечении. Также, благодаря 3D-принтеру проектировать можно не только внешние очертания предмета, но и внутреннее наполнение для изменения его веса.
С 2022 года российские компании работают в сложных условиях: логистические цепочки нарушены, многие западные игроки перестали поставлять компоненты в РФ. Поэтому новая экономическая реальность делает 3D-печать одной из ключевых технологий для процесса импортозамещения.
Что касается подготовки специалистов, то в последние годы в нашей стране появилось много сильных 3D-кафедр в вузах: МГТУ им. Баумана, МАИ, Питерский и Московский политехнические университеты, УГАТУ (Уфа), Национальный исследовательский технологический университет МИСиС, Пермский национальный исследовательский Политехнический университет, Дальневосточный федеральный университет и многие другие.
Эксперты считают, что массовое внедрение АТ кратно ускорит производственный процесс и кардинально изменит методологию управления машиностроением: уйдёт оборот чертежей и любых бумажных носителей, производство будет занимать значительно меньше времени, а коэффициент использования материалов возрастёт.
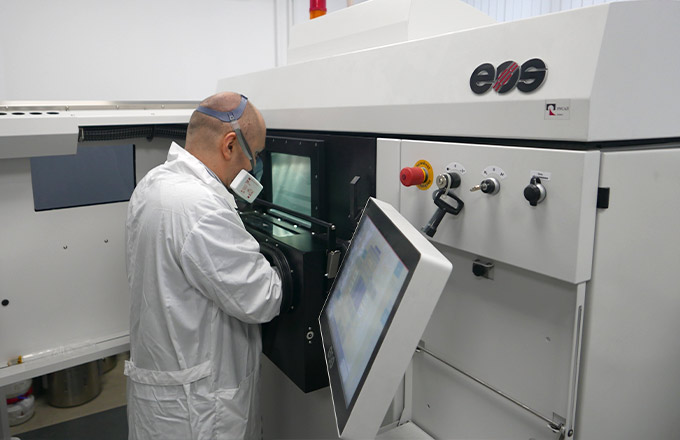
За счёт использования современных подходов моделирования фазового состава, разработчикам ИЛМиТ удалось подобрать оптимальные соотношения легирующих элементов
Ко всему прочему, технологии не стоят на месте. На прошлой неделе в авторитетном журнале Nature Communications вышла статья о разработке европейских и сингапурских учёных, которые придумали новый тип систем трёхмерной печати. Она позволяет не только производить сложные металлические конструкции из разных металлов, но и управлять их внутренней структурой. Это позволит значительно сократить расходы энергии на изготовление металлических изделий.
«Мы выяснили, что лазер можно применять в качестве микроскопического кузнечного молота для обработки металла давлением при работе 3D-принтеров. Этот же лазер можно использовать для повторного плавления металла и релаксации его структуры — это готовит его к структурным изменениям, которые происходят, когда изделие помещают в печь. Мы ожидаем, что этот подход снизит расходы энергии при изготовлении деталей», — цитирует ТАСС ведущего автора работы, доцента Кембриджского университета Маттео Сейта.
Как отмечают Сейта и его коллеги, помимо экономии на процессах производства, система позволит создавать конструкции, состоящие из слоев металла с разными свойствами, идеально подобранными для решения конкретных задач.
Технологию, по словам учёных, можно реализовать на любой системе 3D-печати металлами, оснащённой лазером или возможностью его подключения к устройству. Это говорит о возможности использования систем лазерной 3D-печати для относительно дешёвого и эффективного производства высококачественных металлических изделий.
Егор Петров